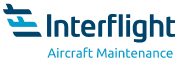
PROJECT REQUIREMENTS
When a regular client asked us to repaint one of their aircraft in late February, we booked in the work with our trusted partner RAS Completions. But what initially seemed like a simple four-week job quickly escalated when we discovered serious corrosion that meant extensive repairs were needed. The project was made even more challenging when the Covid-19 pandemic hit, causing logistical difficulties and delays.
OUR SOLUTION
The corrosion meant several flying control surfaces needed to be repaired or replaced. It was difficult to secure the necessary manpower to complete such a large job during lockdown, but we managed to establish a shift pattern that ensured work could continue around the clock. Many suppliers had been forced to furlough staff and were operating with skeleton crews, creating further delays when sourcing replacement parts.
We needed to replace a cracked elevator part, but a replacement was unavailable and we were told to expect a 22-week lead-time to manufacture a new one. Refusing to give up, our purchasing team utilised their industry contacts and arranged to have the part removed from an aircraft that was still in production, which enabled us to complete the job by July. Once the aircraft was fully repaired, we accompanied the crew on a shakedown flight following the unexpected extended downtime, which it passed with flying colours.
THE FINER DETAILS
Trusted Partners: We were able to draft in support from RAS Completions, a specialist aircraft painting operation based next to our Biggin Hill hangar.
Industry Experts: Our team worked tirelessly to ensure we had enough staff and could source the correct replacement parts. This was a very challenging process and our unrivalled industry contacts and expertise were invaluable in getting the job completed with no further delays.